La naissance des cobots : des robots collaboratifs au service des usines 4.0
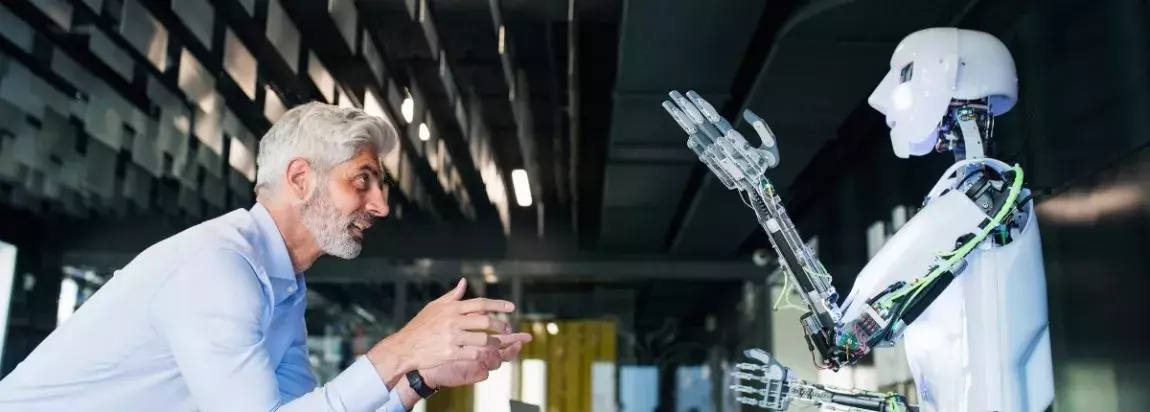
L’industrie 3.0 a été marquée par l’automatisation et la digitalisation des processus industriels. Ainsi, la robotisation est montée en puissance au sein des usines de production. Il a fallu faire face à l’inquiétude grandissante des ouvriers de ce secteur, inquiets quant à la sécurité de leurs emplois dans le secteur secondaire.
Aujourd’hui, grâce à l’industrie 4.0, les usines deviennent connectées. On assiste à l’utilisation grandissante de capteurs (IoT – objets connectés) notamment, et l’automatisation des processus (RPA) se poursuit grâce à l’arrivée de l’impression 3D, de la réalité virtuelle, de l’intelligence artificielle et des jumeaux numériques.
Cette transformation numérique rapide et de grande ampleur reste une opportunité pour les entreprises industrielles. Elles doivent en effet s’adapter et intégrer ces nouvelles technologies au sein de leurs usines. L’enjeu est de rester compétitives, attractives et ainsi gagner en performance sur des marchés en pleine mutation. En ce sens, les PME comme les grands industriels, de tout secteur d’activité (automobile, pharmaceutique, etc.), font maintenant confiance aux cobots.
Les cobots, quèsaco ? Portrait-robot ...
Vous avez bien lu COBOT et non ROBOT... mais de quoi s’agit-il ? (Ce terme est pourtant apparu pour la première fois en 1996).
Un cobot, aussi appelé robot collaboratif, se présente principalement sous forme d’un bras articulé. Il s’intègre parfaitement sur une chaîne de production et est capable de saisir une charge utile de 20kg maximum, de déplacer un objet, de visser des pièces ou de conditionner. Il permet donc d’éviter les manœuvres répétitives, laissant aux humains la possibilité de réaliser les tâches nécessitant plus de précision ou d’expertise. Ainsi, les conditions de travail des ouvriers sont améliorées et les risques de troubles musculo-squelettiques sont limités.
En 2016, le MIT (Massachusetts Institute of Technology) a démontré que la collaboration homme-robot est 85% plus productive qu’un robot ou un humain travaillant seul.
Mais pourquoi investir dans un cobot plutôt qu’un robot ?
Sa grande différence avec le robot classique est qu’il est conçu pour travailler de manière sécurisée dans une zone commune avec un opérateur et ce grâce à ses capteurs et ses caméras intégrées. De plus, il peut être facilement reprogrammé, déplacé et redéployé à différentes étapes de la chaîne de production. En effet, l’opérateur peut lui apprendre de nouvelles tâches qu’il répétera et mémorisera. L’approche d’apprentissage par la pratique est révolutionnaire dans ce secteur et ne cesse d’évoluer. Désormais, il existe des cobots qui, grâce à leurs capteurs, répètent les gestes des ouvriers, sans qu’aucune programmation ne soit nécessaire.
C’est cette flexibilité qui les démarque des robots industriels classiques et qui les rendent attractifs. Retenons tout de même qu’ils peuvent être sujets à des cyberattaques puisqu’il s’agit d’une technologie connectée.
Enfin, il est nécessaire de noter qu’un cobot est moins coûteux qu’un robot classique et les retours sur investissements sont plus rapides, ce qui permet aux PME, notamment, d’investir dans cette technologie.
Un marché porteur pour le secteur industriel
Tout comme de nombreux marchés, le secteur de la cobotique a également été touché par la COVID-19, même si la pandémie a eu quelques effets positifs sur le marché des robots collaboratifs. En effet, cette technologie permet de maintenir les distanciations sociales et respecter les gestes barrières au sein des chaînes de production mais aussi limiter l’absentéisme.
Cependant, les recherches indiquent que la croissance reprendra dès 2021 (17,2% de croissance) et continuera de croître à un taux annuel de 15 à 20% jusqu’en 2028.
D’après cette même source, 15% des ventes de l'industrie de la robotique seront des robots collaboratifs en 2028, de quoi leur assurer un bel avenir.
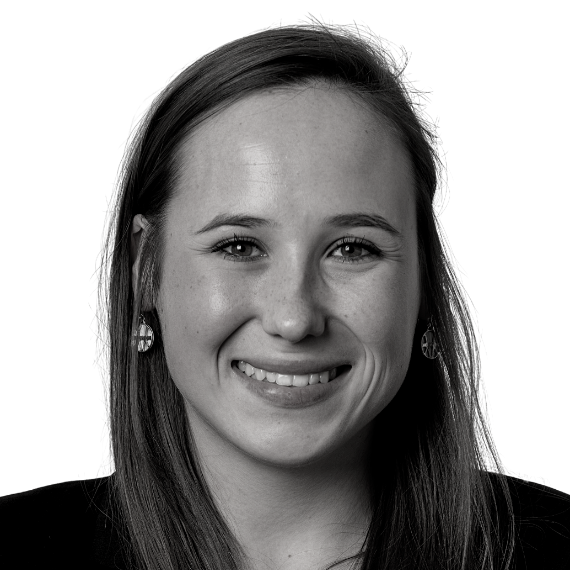