Le machine Learning pour prédire l’usure des outils de coupe
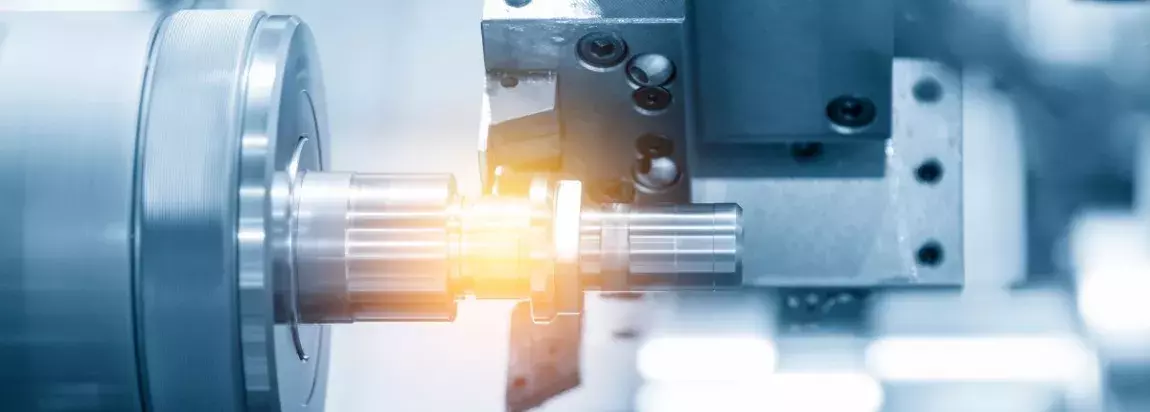
Les industriels cherchent en permanence à optimiser leur production. Plus de rendement, réduction des coûts, tout y passe. Dans cette optique, la gestion des outils de coupe influe sur la qualité des produits usinés mais aussi sur le coût de production.
Comprendre l’évolution de l’usure des outils et donc leur capacité à usiner est crucial. Mais au fait, c’est quoi l’usure ?
Le principe de l’usinage est de faire se rencontrer violemment la pièce que l’on souhaite usiner avec un outil aux formes spécifiques et bien plus résistant que la pièce usinée suivant une trajectoire définie. L’outil va alors arracher de la matière à la pièce et ainsi changer sa géométrie.
Les conditions de pression et de température sont telles que l’outil ne s’en sort pas indemne et se dégrade au fur et à mesure de son utilisation, c’est l’apparition de l’usure. Un outil trop usé voit sa géométrie déformée et cela affecte l’usinage. Pour les usinages qui requièrent une grande précision, parfois au micron soit 10-3 millimètre, cela se traduit souvent par un rejet de la pièce, un rebut.
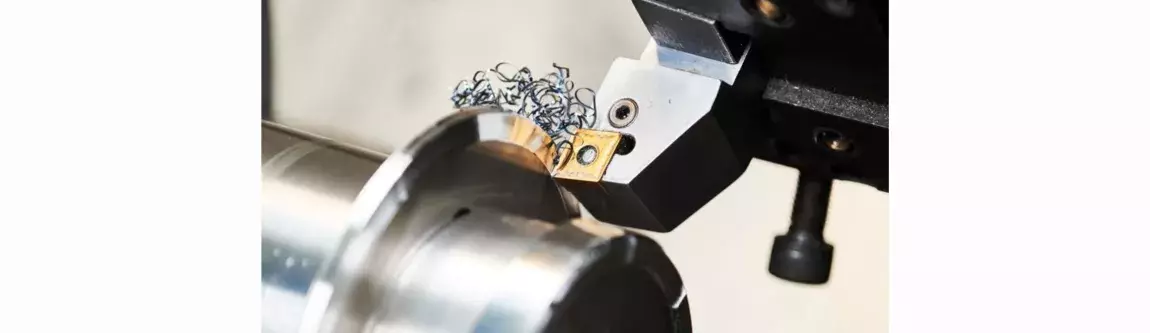
Par ces conditions de pressions et de températures extrêmes, nous pouvons observer des phénomènes physiques apparaître à mesure que l’outil de coupe s’émousse. En effet, un outil de coupe usé nécessitera plus de force pour usiner. Cette force peut se traduire en la variabilité de trois phénomènes :
- Augmentation des vibrations lors de l’usinage
- Déformation accrue des composants de la machine (porte-outil) sous tension
- Augmentation de la puissance délivrée par le moteur
Avec des capteurs modernes, il est possible de mesurer ces variations avec une précision de plus en plus fine. Maintenant, nous avons des données, mais comment les traiter ?
Prédiction de l’usure
Connaître la capacité de ses outils et savoir quand les remplacer n'est pas une chose aisée. Même avec des capteurs, savoir que ma puissance moteur passe de 16 383,7 W à 16 391,5 W entre deux usinages, c’est une belle avancée mais il est difficile d’en tirer quelque chose de fonctionnelle.
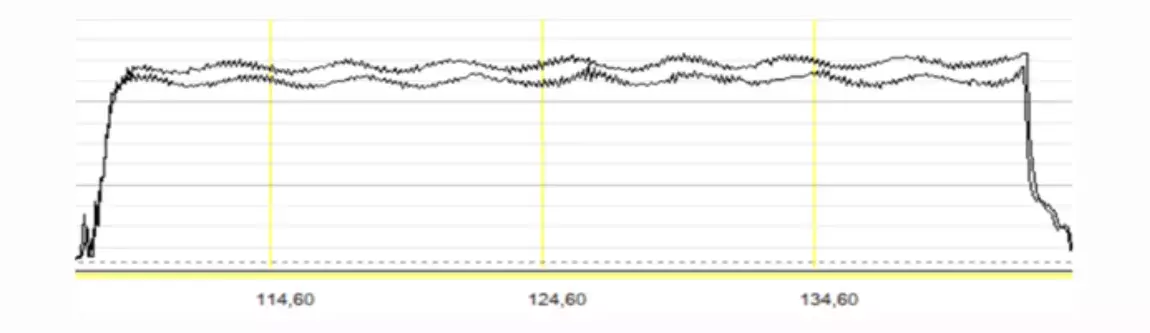
Conclure le niveau d’usure par la simple mesure des phénomènes physiques qui lui sont associés n’est donc pas possible. Il faut donc procéder par apprentissage, c'est-à-dire que l’on relève les valeurs des phénomènes lorsque l’outil est usé. L’opération peut être répétée plusieurs fois pour obtenir une meilleure estimation.
On considère un outil usé lorsque le contrôle de la pièce usinée indique des valeurs proche du seuil de tolérance ou bien directement en analysant les marques d’usure présentent sur l’outil (voir les sources et notamment les parties qui traitent de l’usure en dépouille notée Vb pour approfondir ce sujet).
À présent, nous savons déterminer et prédire l'usure d’un outil mais uniquement lorsque les paramètres de l’usinage sont figés. Il y a 3 paramètres qui peuvent faire varier la durée de vie d’un outil :
- L’outil en lui-même (sa composition, sa géométrie et son revêtement)
- Le matériau usiné (ses caractéristiques)
- Le programme d’usinage (la vitesse de coupe, la profondeur de passe et l’avance outil)
Il faut savoir que dans beaucoup d'industries, ces paramètres peuvent varier d’une machine à une autre, voire d’un usineur à un autre. Changer un paramètre et c’est toute l’opération d’apprentissage qu’il faut recommencer. Alors comment standardiser ?
Les systèmes d’information
Le marché actuel offre plusieurs solutions pour l’acquisition des données mais en ce qui concerne le traitement, il n’existe aucune solution commercialisée qui soit viable. La première raison est la complexité des modèles mathématiques due aux grands nombres de paramètres à prendre en compte. Les quelques solutions existantes sont basées sur l'apprentissage, mais c’est une méthode qui ne tolère pas la variabilité.
L’évolution naturelle de cette méthode par apprentissage serait le Machine Learning. En effet, l’apprentissage nous permet d’acquérir des données sur une configuration. En faisant varier chaque paramètre de cette configuration et en passant les données à travers un réseau neuronal convolutif (RNC), il est possible de développer un système d’information intelligent capable de prédire l’usure d’une autre configuration de paramètres.
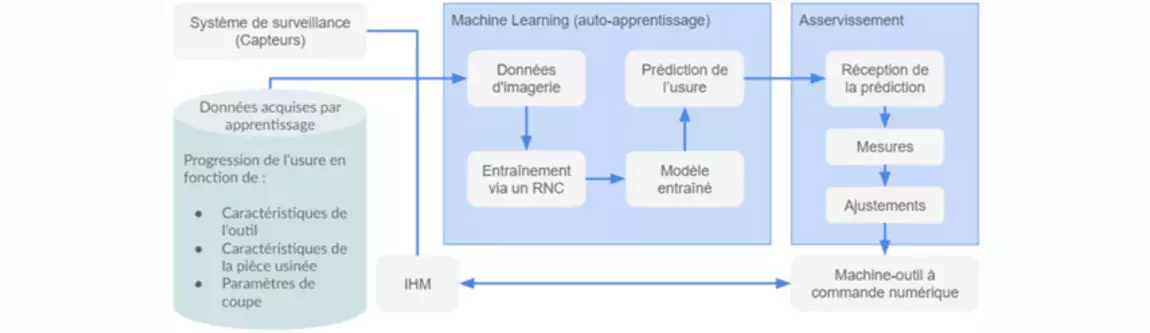
Les intelligences artificielles, le Machine Learning ou encore le Deep Learning sont encore trop peu présentes chez les industriels métallurgiques. Ces technologies vont peu à peu se démocratiser à mesure que les industriels évoluent vers l’industrie 4.0.
Pour en apprendre plus sur l'usure outil et les phénomènes liés :
- Recherche de l’usure de l’outil de coupe lors du tournage d’éprouvettes pour l’essai de traction, BAKHTI Abdelbassit et MERZOUG Aissa
- Modélisation de l’usure par diffusion des outils de coupe en usinage à grande vitesse, Mohammed NOUARI
Le sujet vous intéresse ? Nos experts vous répondent
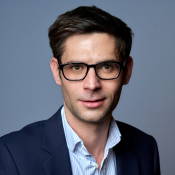
Les nouvelles technologies façonnent l’industrie du futur en une industrie plus agile, plus connectée et plus respectueuse de l’environnement. Notre offre s’appuie sur des consultants expérimentés qui vous accompagnent sur vos problématiques industrielles quelque soit le secteur d’activité pour mettre en place un SI robuste, transparent et modulable.
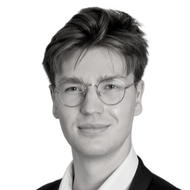