Jumeau numérique, quels avantages pour l’industrie qui télétravaille ?
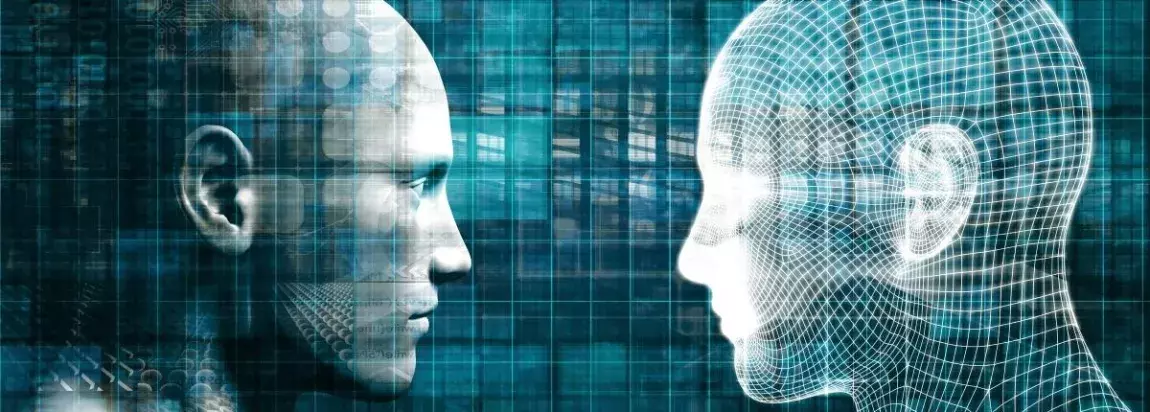
La société d’aujourd’hui se réinvente chaque jour et prône la fluidification des transports, la réduction des émissions de gaz à effet de serre, l’évolution des modes de management, l’équilibre vie professionnel/personnel… Dans un contexte d’une crise sanitaire où le maître mot est « confinement », l’industrie mondiale doit s’adapter. Le leitmotiv du travail de demain dans l’industrie n’est-il pas le télétravail ?
L’ère de la data : le combat de la performance
L’ingénierie moderne entraîne l’accroissement du nombre de simulations effectuées pour développer de nouveaux produits et procédés. Le concept d’industrie 4.0 ouvre la porte à la massification des données, permettant ainsi de planifier les projets. Un des pans de l'industrie 4.0, le Digital Twin, vise à permettre une expertise numérique sur toutes les phases des projets :
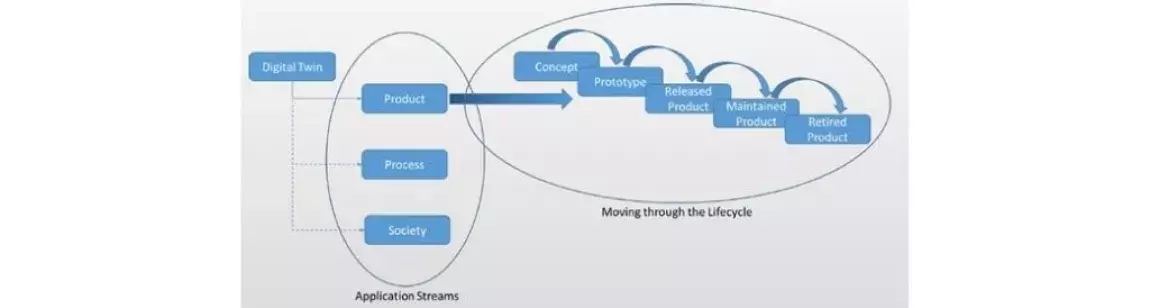
Le Digital Twin vit et se développe sur la base de données d'exploitation. Ces données peuvent provenir du produit physique ou du processus fonctionnant dans le monde virtuel. La data est l’oxygène du Digital Twin, elle lui offre la possibilité d’innover à la vitesse de la pensée. Le jumeau numérique n'assume pas seulement le rôle d'une épine dorsale mais, en temps réel, connecte tous les utilisateurs et leurs informations en un seul environnement pour cultiver une créativité continue, apportant des améliorations dans les produits et processus, ainsi qu’un monitoring instantané sans être dans les locaux industriels face aux machines.
La technologie au service de la conception et des évolutions
Maximiser les performances industrielles n'est pas facile. Dans un contexte de réduction des coûts et des risques liés à l'amélioration des opérations, le Digital Twin offre une simulation dynamique qui modélise les environnements physiques, permettant ainsi d'effectuer des tests avancés. Il y a peu de place pour la conjecture, donc quand il s'agit de savoir ce qui améliorera vraiment vos opérations, la prévoyance peut être inestimable.
L'ingénierie des systèmes a l’opportunité d'influencer les décisions précocement dans la conception et le développement de systèmes. En règle générale, 80% des principales décisions d'ingénierie sont prises dans les 10% du cycle de vie du projet. Une fois conçu virtuellement ce même modèle est utilisable pour l'ingénierie des processus et des systèmes de contrôle, la validation du système de contrôle, la formation des opérateurs sans affecter les processus en cours d'exécution.
En plus de pouvoir faire évoluer les systèmes industriels à distance sans prototype physique, les jumeaux numériques permettent de trouver et tester de nouvelles solutions dans le développement de produits plus rapidement qu’avant. On estime que les simulations numériques ont réduit le délai de livraison au client final de 10 à 20%.
La technologie au service des ouvriers
Le jumeau numérique joue également un rôle clé dans la facilitation du travail des ouvriers. Le Digital Twin combine la capacité de simulation dynamique et l’analyse des données en temps réel, offrant ainsi un monitoring prédictif extrêmement précis et fiable. En s’appuyant sur l'utilisation des données IoT et sur le système virtuel il est possible de diagnostiquer, dépanner, anticiper les pannes ou encore déterminer le point optimal pour la maintenance. Les ouvriers de maintenance peuvent assumer une majeure partie du travail à distance et planifier leurs opérations grâce à l’analyse BI des jumeaux numériques.
Le jumeau numérique rebat les cartes de la formation des ouvriers industriels avec l’aide de la réalité virtuelle (VR) pour aider les futurs opérateurs de machines, de lignes de production ou de produits de consommation. Selon Gas HR Benchmark 2010, il faudrait six à sept ans pour préparer un opérateur d’usine à prendre les bonnes décisions. Avec une durée moyenne de cinq ans ou moins par poste, les opérateurs d'usine passent à d'autres rôles avant d'être compétents dans leur poste actuel. Le Digital Twin permet ainsi, à distance et en autonomie, de réduire le temps de montée en compétence de l'opérateur.
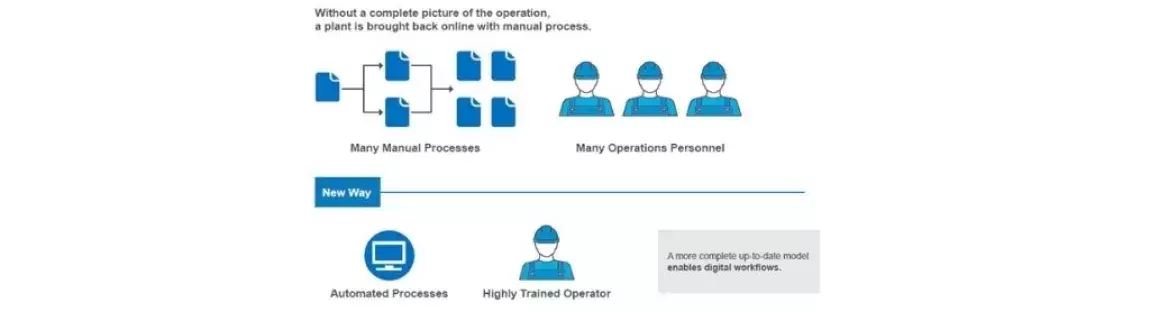
CIMdata estime que la technologie des Digital Twin est, à bien des égards, encore au tout début de son adoption. Une adoption qui semble s’accélérer dans un monde qui change et dans un contexte sanitaire qui s’oriente vers un travail à distance. Le Digital Twin s'adapte efficacement à un travail hors-site pour permettre à l’industrie d’aujourd’hui de voguer vers l’industrie du futur.
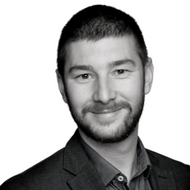